ISO 9001:2015 is the most widely recognized quality management system (QMS) standard in the world, helping businesses of all sizes enhance their operational efficiency and meet customer expectations. Implementing this standard demonstrates a company’s commitment to quality and continual improvement, opening doors to new opportunities and fostering trust among stakeholders.
In this guide, we will explore the essentials of ISO 9001:2015, its benefits, the implementation process, and practical tips to get certified. Whether you are new to ISO standards or looking to upgrade your current QMS, this article provides everything you need to know.
What Is ISO 9001:2015?
ISO 9001:2015 is an international standard for quality management systems, published by the International Organization for Standardization (ISO). It sets out criteria to ensure that organizations consistently deliver products and services that meet customer and regulatory requirements.
The 2015 revision of the standard introduced a risk-based approach, emphasizing:
- Leadership involvement
- Contextual understanding of the organization
- Process efficiency
- Continual improvement
ISO 9001:2015 applies to any organization, regardless of its size or industry, making it a universal framework for achieving operational excellence.
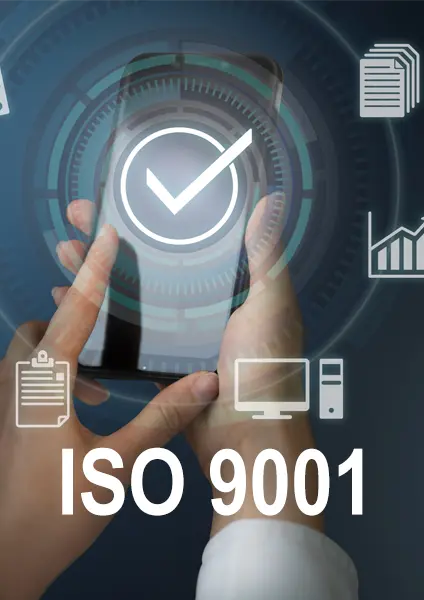
Why Is ISO 9001:2015 Important?
Achieving ISO 9001:2015 certification signals that your organization prioritizes quality, efficiency, and customer satisfaction. Here are some of its key benefits:
Improved Customer Satisfaction
ISO 9001:2015 emphasizes understanding customer needs and exceeding their expectations. This focus leads to higher satisfaction rates and stronger customer relationships.
Enhanced Efficiency
By streamlining processes and identifying inefficiencies, ISO 9001:2015 helps organizations save time and reduce costs.
Competitive Advantage
Certification demonstrates your commitment to quality, giving you an edge in competitive markets and often being a prerequisite for bidding on contracts.
Risk Management
The risk-based approach helps identify potential issues before they arise, allowing businesses to take proactive measures.
Global Recognition
As an internationally recognized standard, ISO 9001:2015 enhances your reputation and opens up opportunities for global trade.
Key Principles of ISO 9001:2015
The standard is built on seven principles that guide its implementation:
- Customer Focus: Understanding and meeting customer needs.
- Leadership: Strong leadership fosters a culture of quality.
- Engagement of People: Involvement of employees at all levels.
- Process Approach: Efficiently managing interrelated processes.
- Improvement: Ongoing enhancement of QMS performance.
- Evidence-Based Decision Making: Using data to inform decisions.
- Relationship Management: Managing relationships with stakeholders.
Steps to Implement ISO 9001:2015
- Understand the Standard
Begin by thoroughly reviewing the ISO 9001:2015 requirements. Consider taking a training course or consulting with an ISO expert.
- Conduct a Gap Analysis
Assess your current processes against the standard to identify areas that need improvement.
- Develop a Quality Policy and Objectives
Define a quality policy that aligns with your business goals and establish measurable objectives.
- Document Your QMS
Create or update documentation, including:
- Quality manual
- Standard operating procedures (SOPs)
- Work instructions
- Train Employees
Educate your team on ISO 9001:2015 principles and their roles in maintaining the QMS.
- Implement Changes
Put your documented processes into practice, addressing gaps identified in the analysis phase.
- Conduct Internal Audits
Regularly review your QMS to ensure compliance and identify improvement opportunities.
- Certification Audit
Engage a third-party certification body to audit your QMS. Address any non-conformities to achieve certification.
Practical Tips for ISO 9001:2015 Certification
- Get Leadership Support
Ensure top management is fully committed to the certification process, as their involvement is crucial for success.
- Focus on Employee Engagement
Actively involve employees in the development and implementation of the QMS to foster ownership and accountability.
- Keep It Simple
Avoid over-complicating processes and documentation. Focus on creating a system that works for your organization.
- Leverage Technology
Use software solutions to automate QMS processes, streamline document control, and simplify audit management.
- Monitor and Measure
Regularly measure your performance against established objectives to identify areas for improvement.
Common Challenges and How to Overcome Them
- Resistance to Change
Overcome resistance by communicating the benefits of ISO 9001:2015 and involving employees in the process.
- Lack of Resources
Ensure adequate resources, including time, budget, and personnel, are allocated for implementation.
- Documentation Overload
Streamline documentation by focusing on what is essential and avoiding unnecessary paperwork.
Case Study: Successful Implementation
ABC Manufacturing Co. implemented ISO 9001:2015 to enhance their production quality. By standardizing processes and adopting a risk-based approach, they reduced defects by 25% within a year. The certification also helped them secure contracts with international clients, boosting revenue by 30%.
Conclusion
ISO 9001:2015 is more than just a certification; it’s a strategic tool that drives business growth, enhances efficiency, and improves customer satisfaction. Whether you’re aiming to increase market share or streamline operations, adopting this standard can transform your organization.
Start your journey toward ISO 9001:2015 certification today to unlock its full potential and stand out in a competitive marketplace.
Certification Process
1- Completion of information related to the company name, company activities, the number of staff per work shift, website address, and branches.
2- Announcement of costs related to the requested certification issuance process.
3- Preparation and approval of the contract for implementation.
4- Planning the audit process and notifying the client for audit process.
5- reviewing documents to identify the client strengths and weaknesses in comparison to the established documentation.
6- Corrective actions for potential weaknesses.
7- Final planning for conducting the audit, registration, and certification issuance.
8- Conducting the on-site audit process at the client by the specialized team of the certifying company.
9- Corrective actions for potential weaknesses in the execution of the organization’s processes.
10- Recommendation for the issuance of a certification related to the client to the head office.
11- Achieving the related certification.
12- Renew after three years.
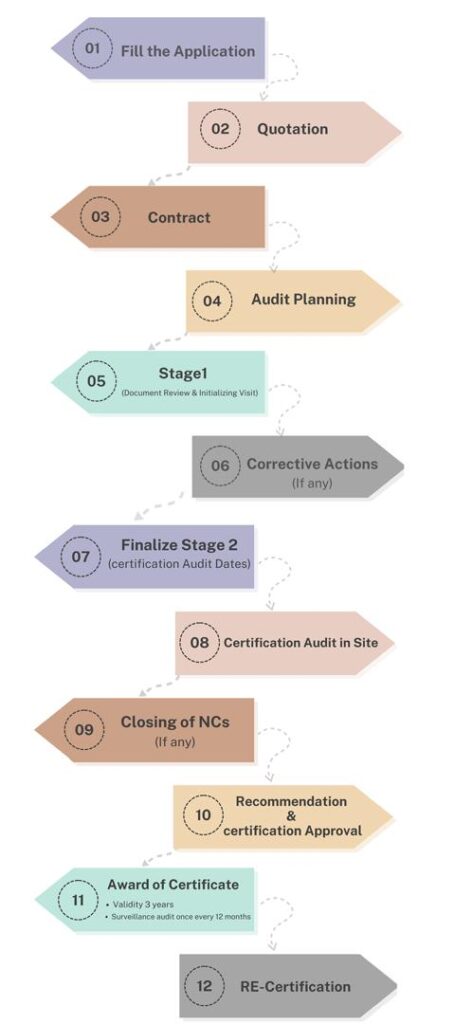